Damage to pipes connected to the main primary system of EDF reactors caused by stress corrosion
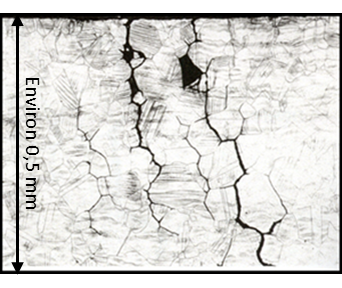
EDF has detected damage to pipes connected to the main primary system of some reactors, caused by stress corrosion. This information report explains what stress corrosion is and how to detect it.
Just what is stress corrosion?
Stress corrosion cracking (SCC) is a fairly frequent phenomenon in industry in general (excluding the nuclear industry), which is characterized by cracking in a material in contact with a chemical environment. Stress corrosion cracking is generally caused by a combination of mechanical stresses and an aggressive environment affecting sensitive material. This damage initiates one or several cracks, which then spread within the material, as shown in the figure opposite illustrating SCC cracks on stainless steel in contact with the primary coolant.
In the nuclear industry, the stainless steels used to manufacture the main cooling systems and connected systems consist of iron, alloyed with chromium and nickel; these steels are barely sensitive to SCC in pressurized water reactor (PWR) primary water environment. If stress corrosion cracking occurs, it is mainly due to tensile stresses in the material, or unexpected coolant contamination. The chemical composition of the coolant used in the primary reactor system is closely monitored.
Stresses are caused by manufacturing operations, particularly welding, and operating conditions. In order to minimize stresses, manufacturers develop welding processes which precisely define the applicable parameters, e.g. the intensity of the welding current.
The basic driving mechanism behind SCC is probably metal oxidation, activated by temperature. On this basis, the higher the temperature, the earlier cracking starts and the faster the cracks spread, for a given mechanical load and chemical environment.
SCC is particularly pernicious as it can only be detected after an incubation period, which can last up to several decades. SCC can only be detected after cracking has initiated, i.e. SCC will not be identified in regular piping inspections until a defect occurs. The approximate order of magnitude of crack propagation rates observed in SCC vary, and can reach up to one millimetre per year.
Stress corrosion cracking is unusual in stainless steels, in PWR primary water environment, however some SCC occurrences have already been observed for PWRs. Approx. 150 cases have been identified worldwide in the last thirty years, on primary systems or systems connected to the latter. Reactors with various operating lifetimes have been affected, caused by a wide range of factors.
Considering the stakes inherent in such damage, IRSN has sought methods aiming to reproduce SCC on stainless steels in the primary environment in laboratory conditions for many years. The aim is to identify the chemical and metallurgical conditions which promote stress corrosion cracking.
Non-destructive testing: what techniques are available?
Defects in pipes can be detected using Non-Destructive Testing (NDT) techniques. A wide range of NDT techniques are available, and fall into two categories: volumetric techniques, used to detect defects deep inside the part (Ultrasonic Testing [UT], Radiographic Testing [RT]), and surface NDT methods used to detect surface defects (e.g. Eddy Current Testing [ET] or Penetrant Testing [PT]). These techniques can be combined to optimize the detection and characterization of SCC cracks of just a few millimetres, deep inside the stainless-steel pipes.
One of the most frequently used NDT technique for in-service monitoring in the nuclear industry is UT. This technique does not emit ionizing radiation, unlike RT, and can be performed on a pipe filled with water, while the sensitivity of RT is reduced in this configuration. The underlying physical principle is relatively simple and similar to medical ultrasound. During propagation, if the ultrasonic wave hits a discontinuity (e.g. a crack), it is reflected, and its echo is recorded and then analyzed by the specialist. However, stainless steel parts may be challenging to inspect during propagation, the ultrasonic waves interact with the specific metallurgical structure of stainless steel and a series of ultrasonic echoes may be reflected from the metallurgical structure. This phenomenon is known as structural noise. In this case, the echo reflected by a crack can be masked by structural noise. The priority for the UT specialist is to differentiate between a secondary echo caused by structural noise or a geometrical artefact such as one produce by the pipe counterbore and an echo attributable to a crack. The performance of ultrasonic testing has significantly improved in recent years thanks to the development of phased array techniques, ensuring that smaller dimensional defects can be detected.
IRSN contributes to R&D programs in cooperation with international partners, such as the US-Nuclear Regulatory Commission aiming to improve the understanding ultrasonic propagation in stainless steels and to improve the detection and characterization of flaws. One significant outcome of these research programs is a better evaluation of the performance of non-destructive testing for stainless steel inspection and this contributes to an independent and in-depth expertise ability for IRSN.
Download IRSN information note of January 20, 2022: Damage to pipes connected to the main primary system of EDF reactors caused by stress corrosion (PDF)